Bincen Belt Scales Used for Modern Material Handling
Traditional methods, such as manual weighing and batching systems, can lead to human error. That’s where electronic belt scales come into play. These devices provide real-time data with high accuracy. This article will look at the many advantages electronic belt scales have over traditional methods and how they can help you optimize your operations.
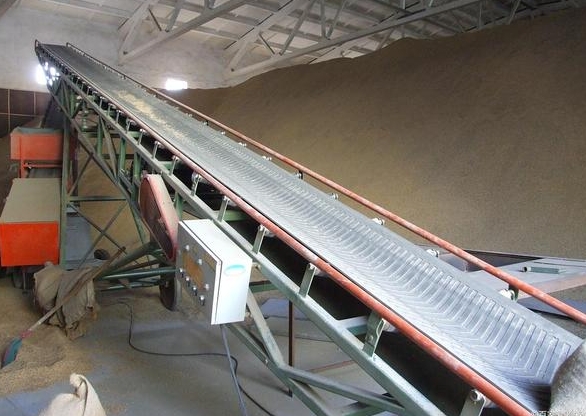
What Are the Electronic Belt Scale Benefits over Traditional Methods?
Electronic belt scales provide a significant improvement in material handling over traditional methods such as manual weighing or batching systems. Here’s a detailed breakdown of the benefits that electronic belt scales provide.
Advantages | Traditional methods | Electronic belt scale benefit |
Real-Time Measurement and Efficiency | Need to stop the flow of material at regular intervals. This causes downtime, disrupts production flow, and may result in inaccuracies due to human error or incomplete batch filling. | Provide continuous measurement of material weight as it moves along the conveyor belt. This enables real-time data on material flow, allowing for immediate adjustments and optimizations. Production efficiency is increased by eliminating downtime and ensuring a consistent, uninterrupted process. |
Enhanced Accuracy and Reduced Waste | Human error in reading scales can result in significant inaccuracies. Inaccurate measurements can lead to material waste, under- or overfilling of products, and billing errors. | It is highly accurate, ranging from +/- 0.125% to 5% depending on the model and application. This level of precision ensures that each gram or pound of material is precisely measured, reducing waste, ensuring consistent product weight, and providing reliable data for accurate billing. |
Versatility and Adaptability | Frequently limited to specific material types. Batching systems may need to be modified or adjusted to accommodate different materials. This may be time-consuming and inconvenient. | Designed to handle a variety of bulk materials. From fine powders like flour and grains to large rocks and aggregates, electronic belt scales can handle it all. They can also adapt to varying flow rates, making them suitable for a wide range of applications across industries. |
Durability and Reliability | May need frequent maintenance or replacement due to wear and tear, particularly in demanding industrial environments. | Designed to withstand harsh industrial conditions. They are resistant to dust, moisture, and extreme heat. This sturdy design ensures dependable operation with little downtime for maintenance, maximizing productivity. |
Integration and Automation Potential | Data logging and integration with control systems can be laborious and time-consuming. Batching systems may necessitate manual adjustments based on weight measurements. | Work seamlessly with control systems. They provide data in real time that can be used to automate and control processes. This enables automatic adjustments to material feed rates, triggering other equipment based on weight measurements, and resulting in a more streamlined production process. |
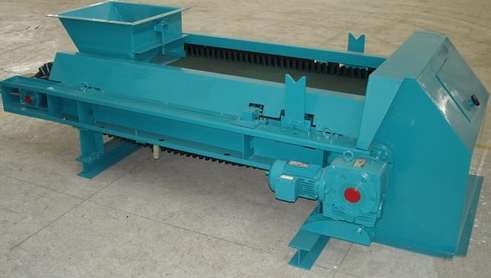
Electronic Belt Scale Provided by BINCEN
Feature | Speed Regulating and Batching Belt Scale | Measuring Belt Scale | Quantitative Belt Feeder | Screw Feeder |
Definition | An electronic belt scale that can adjust the conveyor belt speed to achieve a specific feed rate or batch weight. | A type of electronic belt scale used to determine the mass flow rate of bulk materials. | A feeding device that uses an electronic belt scale to regulate the flow rate of bulk materials. | A feeding device that uses a screw to convey and measure bulk materials. |
Operation | The weight controller continuously monitors the weight of material on the belt and adjusts the belt speed as needed to maintain the desired feed rate or achieve the target batch weight. | The total mass of material conveyed is calculated by multiplying the weight of material on the belt by the speed of the belt. | Uses an electronic belt scale to control material feed rate, ensuring accurate and consistent dosing results. | Uses a screw to convey material at a controlled rate, which is usually set by adjusting the screw speed. |
Applications | Batching applications, packaging lines, and loading stations. | Continuous weighing, process control, and material tracking. | Precision feeding, blending, and dosing. | Feed powders, granules, and other dry bulk materials |
Advantages | Accurate batching, consistent feed rates, and lower material waste | High precision, real-time weight data, suitable for a wide range of materials. | Precise control over feed rate and consistent product quality | Simple design, low maintenance, and cost-effective. |
Electronic belt scales are a versatile and accurate method for determining the mass flow rate of bulk materials. Speed-regulating and batching belt scales are ideal for applications that require precise batching or controlled feed rates. Measuring belt scales are ideal for continuous weighing and process control. Quantitative belt feeders ensure accurate and consistent dosing of bulk materials. Screw feeders are a simple and cost-effective way to feed dry bulk materials. The most appropriate type of feeding device is determined by the application’s specific requirements, material properties, and budget constraints.
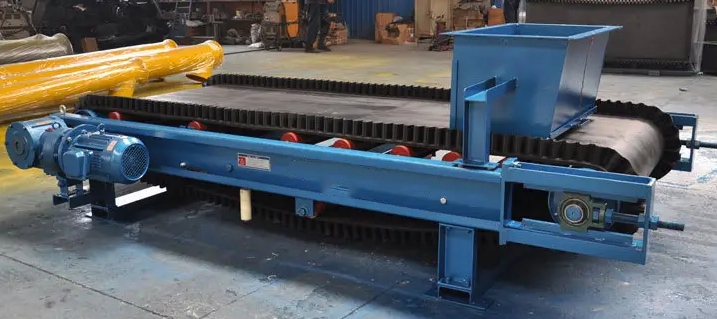
Conclusion
Businesses can benefit greatly from replacing outdated methods with electronic belt scales. From real-time measurement and waste reduction to increased versatility and seamless integration with automation systems, electronic belt scales enable a new level of efficiency and control. BINCEN’s electronic belt scales, which are designed for dependability and accuracy, are the ideal solution for your specific material handling requirements. By selecting BINCEN, you can ensure a future of optimized processes, lower costs, and a safer workplace.