A Guide to Industrial Filling Scale Calibration and Preventative Maintenance
Maintaining accurate and reliable industrial filling scales is crucial for any business that relies on precise product measurement. Inconsistent or inaccurate filling can lead to product giveaways, customer dissatisfaction, and even legal repercussions. This guide will delve into the importance of filling scale calibration and preventative maintenance, ensuring your equipment functions optimally.
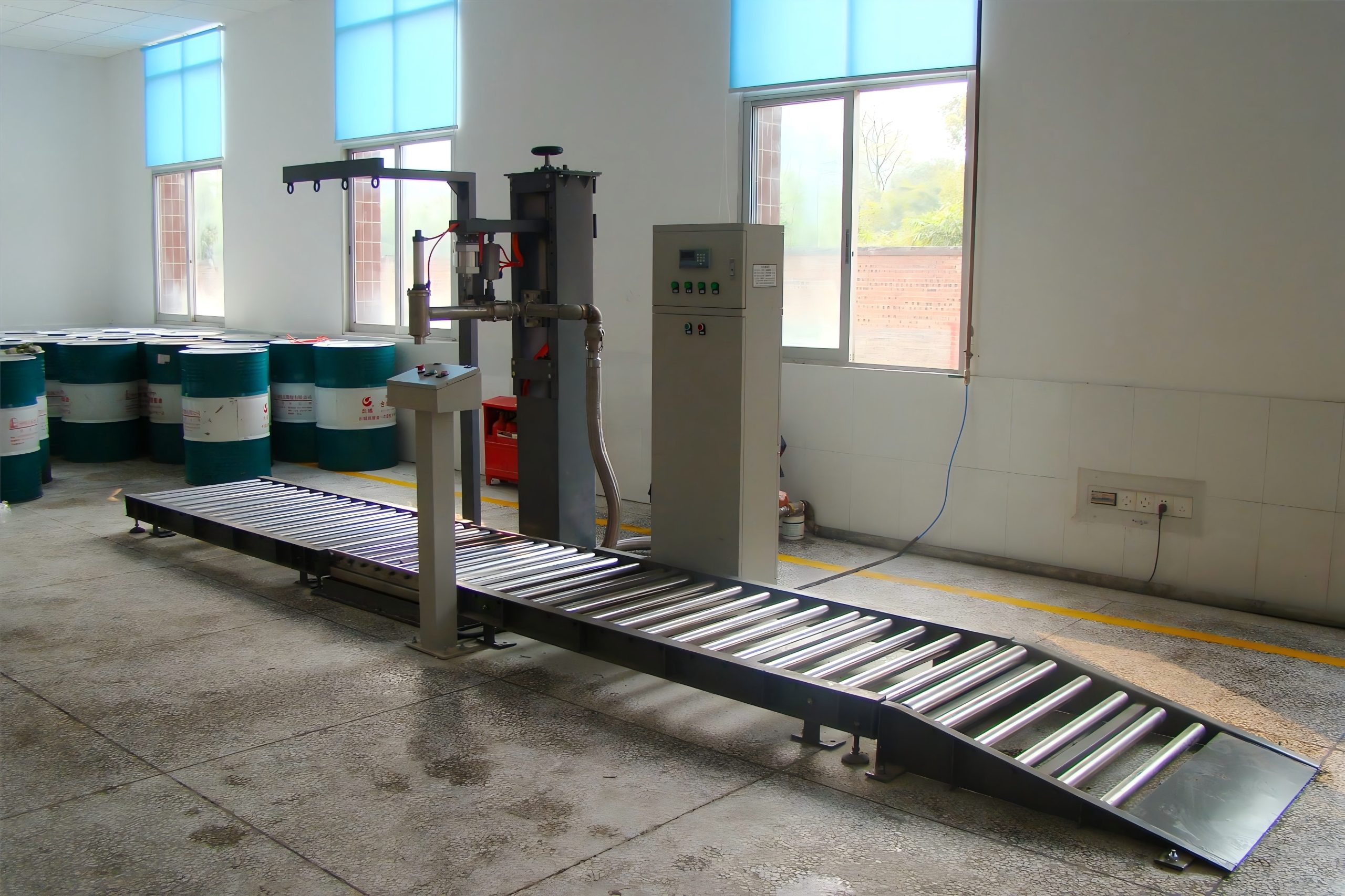
Understanding Filling Scale Calibration
Calibration is the process of verifying and adjusting the accuracy of a filling scale. It’s essentially a checkup for your scale’s performance. Imagine it like calibrating a thermometer – you’re comparing its readings against a known standard (boiling water at 100°C) to ensure it reflects the true temperature. Similarly, during filling scale calibration, we compare the scale’s readings against a known weight standard. This standard typically comes in the form of certified test weights with traceable weight certificates. By comparing the scale’s displayed weight for each test weight with the actual weight of the standard, we can identify any discrepancies. Regular calibration helps mitigate the effects of wear and tear, environmental factors (like temperature fluctuations), and natural drift that can subtly affect a scale’s accuracy over time. By catching these discrepancies early and making necessary adjustments, we ensure your filling scale consistently delivers the correct amount of product, safeguarding your business from product giveaways and ensuring customer satisfaction.
The Filling Scale Calibration Process
The specific calibration process may vary depending on the type and complexity of your filling scale. However, some general steps are typically involved:
Understanding Filling Scale Calibration
Calibration is the process of verifying and adjusting the accuracy of a filling scale. It’s essentially a checkup for your scale’s performance. Imagine it like calibrating a thermometer – you’re comparing its readings against a known standard (boiling water at 100°C) to ensure it reflects the true temperature. Similarly, during filling scale calibration, we compare the scale’s readings against a known weight standard. This standard typically comes in the form of certified test weights with traceable weight certificates. By comparing the scale’s displayed weight for each test weight with the actual weight of the standard, we can identify any discrepancies. Regular calibration helps mitigate the effects of wear and tear, environmental factors (like temperature fluctuations), and natural drift that can subtly affect a scale’s accuracy over time. By catching these discrepancies early and making necessary adjustments, we ensure your filling scale consistently delivers the correct amount of product, safeguarding your business from product giveaways and ensuring customer satisfaction.
The Filling Scale Calibration Process
The specific calibration process may vary depending on the type and complexity of your filling scale. However, some general steps are typically involved:
Step | Description | Purpose |
Preparation | * Cleaning: Thoroughly clean the scale platform, load cell area, and surrounding environment to remove dirt, debris, or product residue. * Inspection: Conduct a visual inspection to identify loose connections, damaged cables, or physical wear on components. | Minimizes external factors affecting weight readings and identifies potential issues early. |
Warm-up | Allow the scale to power on and stabilize to its operating temperature. | Ensures consistent performance during calibration. |
Test Weights | Use certified test weights with traceable weight certificates covering the scale’s entire weighing range. | Provides accurate weight standards for comparison. |
Data Recording | Technicians meticulously record the scale’s readings for each test weight. | Captures data to identify discrepancies between expected and actual weight. |
Adjustment (if needed) | If discrepancies are found, qualified technicians make fine adjustments to the scale’s internal calibration settings. | Brings the scale back into alignment with known weight standards. |
Documentation | Generate a comprehensive calibration report including: * Date and time of calibration * Identification of scale and test weights used * Recorded data for each test weight * Any adjustments made * Technician name and signature | Provides a record for future reference, demonstrates compliance, and tracks historical performance. |
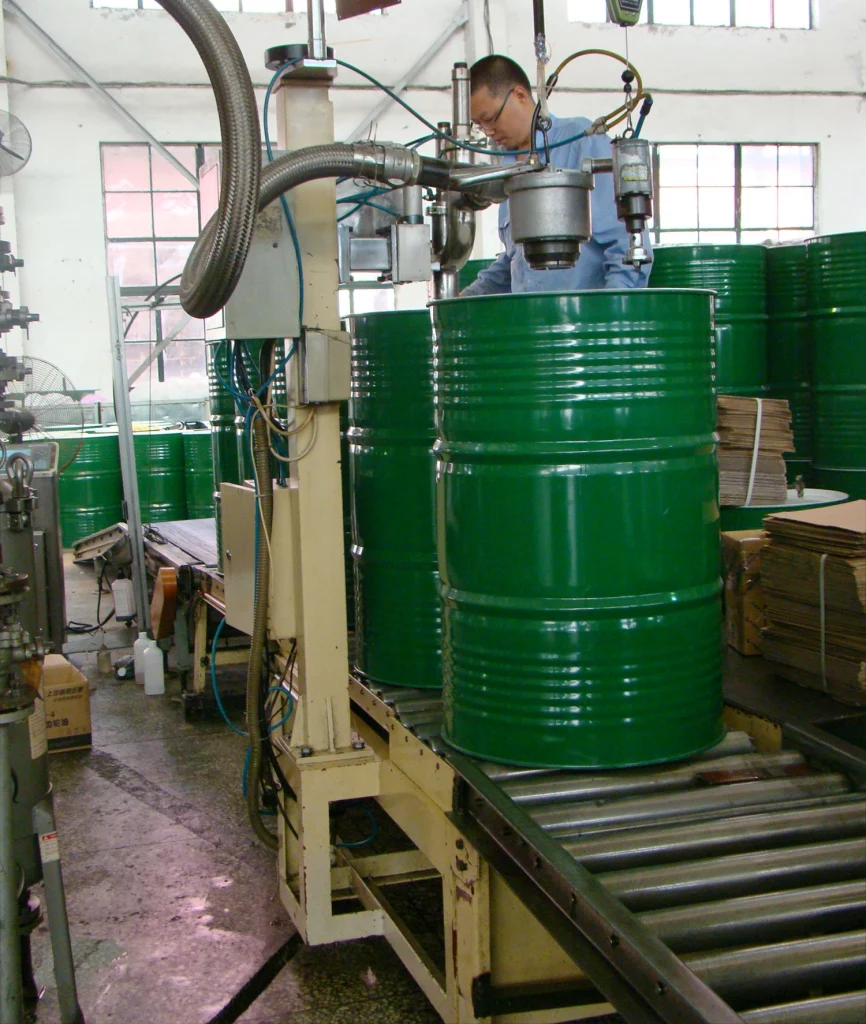
Preventative Maintenance for Filling Scales
Preventative maintenance is a proactive approach to upkeep and care that aims to prevent equipment failure and maintain optimal performance. For filling scales, which are integral to precise measurement and dispensing operations in various industries, implementing a comprehensive maintenance plan is essential to ensure accuracy, reliability, and longevity. Bincen gives you a detailed look at key preventative maintenance practices for filling scales:
- Regular Inspection: Regular visual inspections are vital for identifying potential issues early on. Maintenance personnel should inspect the scale for signs of wear, damage, or contamination. This includes examining load cells, sensors, cables, display units, and other components for any anomalies. Any abnormalities should be promptly addressed to prevent further damage and maintain accurate measurements.
- Cleaning and Lubrication: Proper cleaning and lubrication are essential for keeping filling scales in optimal condition. Dust, debris, and product residues can accumulate on the scale’s surface, affecting its accuracy and functionality. Regular cleaning using appropriate cleaning agents and techniques helps prevent buildup and ensures accurate readings. Additionally, lubricating moving parts such as bearings, pivot points, and slides reduces friction, minimizes wear, and extends the scale’s lifespan.
- Calibration Schedule: Establishing a regular calibration schedule is critical for maintaining the accuracy of filling scales. Calibration should be performed at predefined intervals based on usage, environmental conditions, and industry standards. A well-defined calibration schedule ensures that the scale consistently meets accuracy requirements and regulatory compliance. Calibration procedures should be conducted by qualified personnel using calibrated standards and traceable equipment.
- Software Updates: Filling scales equipped with electronic components and software require periodic updates to ensure optimal performance. Manufacturers often release firmware updates and software patches to address bugs, enhance functionality, and improve accuracy. It’s essential to stay informed about available updates and regularly install them according to the manufacturer’s recommendations. Additionally, software updates may include new features or enhancements that can further optimize scale performance and efficiency.
- Environmental Considerations: Environmental factors such as temperature, humidity, vibration, and electromagnetic interference can impact the accuracy and reliability of filling scales. Monitoring and controlling environmental conditions in the scale’s operating environment help minimize these effects. Installing the scale in a stable and controlled environment, away from sources of vibration and electromagnetic interference, can significantly improve accuracy and reduce the risk of errors.
Implementing a proactive preventative maintenance program for filling scales is crucial for minimizing downtime, ensuring accurate measurements, and optimizing operational efficiency. By regularly inspecting, cleaning, calibrating, updating software, and controlling environmental factors, organizations can maximize the lifespan and performance of their filling scales, ultimately enhancing product quality and customer satisfaction.
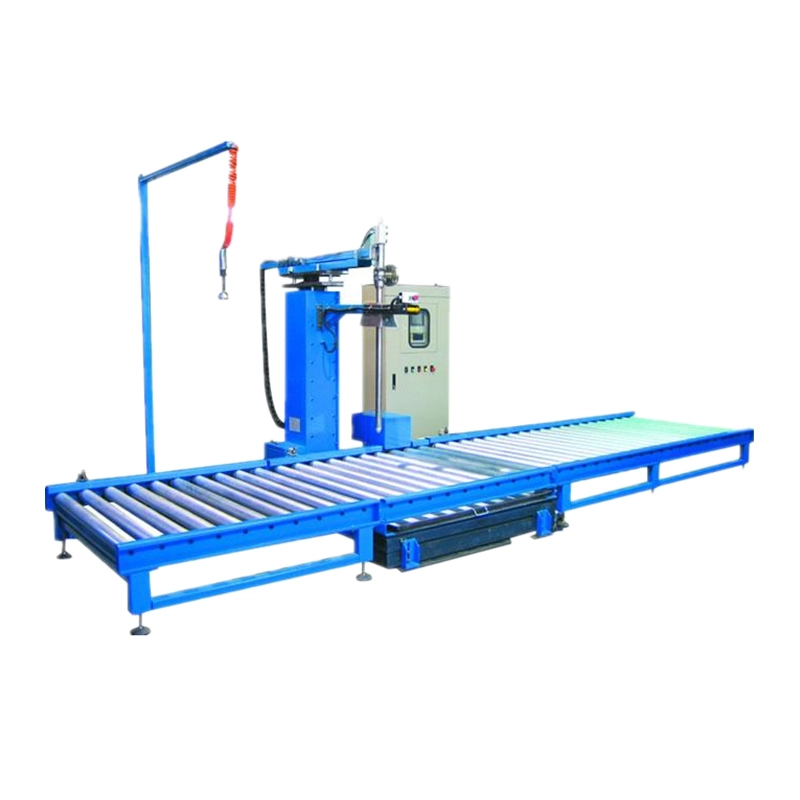
Troubleshooting Common Filling Scale Issues
Even with regular calibration and preventative maintenance, industrial filling scales can encounter occasional problems. Here’s a breakdown of some common issues and steps you can take to address them:
Inaccurate Readings
The first line of defense for inaccurate weight readings is recalibration. Review the calibration report to identify any trends or outliers that might suggest a recurring issue. If the problem persists after recalibration, further troubleshooting is necessary. Many scales display error codes to pinpoint specific problems. Consult the user manual for troubleshooting steps associated with the displayed code. Common errors might indicate malfunctioning sensors, communication issues, or overloaded weight capacities. In some cases, sudden changes in temperature or humidity can affect scale accuracy. Review the scale’s specifications and ensure the operating environment falls within the recommended parameters.
Inconsistent Filling
Inconsistent filling can stem from several factors. Blockages or leaks within the filling system can lead to uneven product delivery. Inspect filling lines, nozzles, and valves for any obstructions or signs of wear. Ensure proper product flow by addressing any identified issues. Other components within the filling system, such as pumps or flow meters, could be malfunctioning. Check for proper operation of these components and perform necessary maintenance or repairs if needed. Vibrations or drafts in the filling environment can disrupt the scale’s stability and lead to inconsistent readings. Isolate the scale from potential sources of vibration and ensure the surrounding area is free from air currents.
Equipment Failure
If the scale becomes completely unresponsive or displays erratic behavior, cease operation and contact a qualified service technician for repairs. Avoid attempting to fix complex issues yourself, as this could further damage the equipment and compromise safety. Regularly scheduled preventative maintenance can help identify and address minor issues before they escalate into equipment failures.
By implementing a proactive approach to troubleshooting, you can minimize downtime associated with filling scale issues and ensure your production line operates efficiently and accurately. Remember, if the problem persists or seems beyond your expertise, seeking assistance from a qualified service technician is crucial to maintaining optimal scale performance.
Conclusion
In the industrial setting, filling scales are indispensable tools for accurate measurement and dispensing of materials. Proper calibration and preventative maintenance are essential to ensure their reliability and precision. By understanding the calibration process, implementing preventative maintenance practices, and addressing common issues, organizations can maximize the performance and longevity of their filling scales, ultimately improving efficiency and product quality.